Sponsored article
The most important information about PVC welding
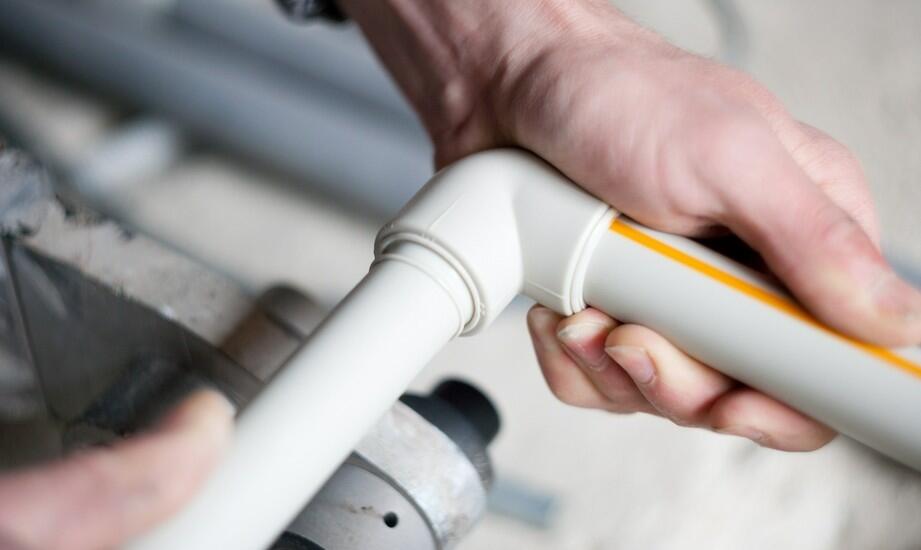
PVC (polyvinyl chloride) welding is a process that allows for permanent and tight joining of elements made of this material. This technique is widely used in various industries, such as the packaging industry, advertising production and the production of transparent film elements. Thanks to its versatility and efficiency, PVC welding allows for the creation of durable and high-strength assemblies.
PVC welding methods
Various methods are used in PVC welding, depending on the specific characteristics of the material. One of the most popular is thermal welding, which involves heating the material to the appropriate temperature and then joining it under pressure. Another method is high frequency welding, a process that uses electricity to create heat in the place of joining. A PVC welder that uses this technology is an excellent solution for the production of packaging and other PVC products. It is characterised by precise and durable joints, and is therefore widely used in many industries.
Key welding parameters
In order to achieve a durable joint, the welding parameters must be precisely adjusted. The most important are temperature, time and pressure. A PVC welder using high frequency requires precise setting of the electromagnetic field power and operating time to ensure the right amount of heat in the place of welding and to avoid material degradation. The welding time depends on the thickness of the material, and the right pressure ensures an even joint without damaging the surface. The PVC welder must be properly adjusted to the material to achieve optimal results.
Application of PVC welding
PVC welding is used in many areas. In construction, it is used to connect protective elements such as roof membranes or swimming pool covers. In the packaging industry, it is used to produce airtight bags and other packaging. In advertising, PVC is used to create banners and tarpaulins. The PVC welder is also used in tent production. The versatility of this method makes it indispensable in many production processes.
Advantages and challenges of PVC welding
PVC welding offers many advantages, such as high durability of joints and resistance to humidity. This process allows materials of different thicknesses and shapes to be joined. A PVC welder ensures solid joints that can withstand difficult operating conditions. The challenges of PVC welding are the need for precise parameter settings and the use of suitable equipment, which requires experience. Zemat Technology Group machines make the PVC welding process precise, which results in high-quality and durable joints.